Production de béton cellulaire: aperçu de la chaîne
La production de béton cellulaire en tant qu'entreprise est récemment devenue très populaire. La raison est assez simple: une technologie relativement simple permet de produire des matériaux de construction de haute qualité, et la demande de matériaux sur le marché contribue à accroître la rentabilité.

Préparation à la production
Matières premières
Ainsi, si vous décidez de commencer à produire des blocs de béton cellulaire à l’échelle industrielle, la première chose à prendre en compte est la matière première. Pour la fabrication de matériaux de haute qualité, il est très important que tous les composants inclus satisfassent aux exigences réglementaires, faute de quoi la qualité opérationnelle des produits sera extrêmement discutable.

Lors de la préparation du mélange, à partir duquel nous allons fabriquer des blocs de construction en béton cellulaire, utilisez les composants suivants:
- De l'eau On préfère boire, qui ne contient ni impuretés ni autres composants. Il est également permis d'utiliser du fluide technique et de l'eau provenant de réservoirs ouverts d'une salinité maximale de 5 000 mg / l.
- L'eau nécessaire à la préparation de la solution doit être conforme aux exigences de la norme GOST 23732-79: elle ne doit contenir ni huiles, ni produits pétroliers, ni grosses particules mécaniques, etc. La rigidité optimale est faible ou moyenne.
Faites attention! Pour augmenter l'efficacité de la réponse, le liquide est chauffé à 45 - 550C.
- Ciment Portland M400 - M500. Il est souhaitable d'utiliser des formulations sans additifs minéraux, avec une structure stable et des indicateurs de qualité satisfaisants. Les ciments pouzzolaniques sont rarement utilisés dans la fabrication du béton mousse.
- La charge est du sable avec une taille de particule d'au plus 1,5 et une teneur minimale en matière organique. Vous devriez également choisir des espèces avec une petite quantité de particules d'argile.
- En plus du sable, vous pouvez utiliser de la farine de chaux ou de dolomie, de la cendre, du laitier de haut fourneau. Lors de la préparation, tous ces matériaux sont broyés à une taille maximale de 0,25 mm.
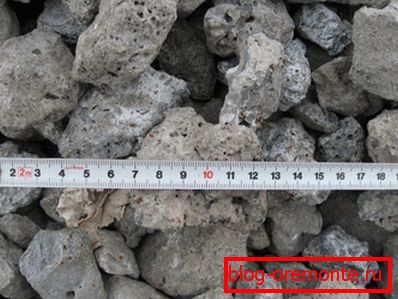
Un agent moussant (poudre d’aluminium ou composition organique d’origine protéique) et des agents de modification sont également des composants importants de la fabrication des blocs de mousse de construction. Le choix des additifs modificateurs peut augmenter considérablement le taux de polymérisation de la composition et améliorer les caractéristiques mécaniques des modules finis.
Si nous parlons de l’amélioration du mélange, il convient de mentionner la fibre parmi les composants utilisés à cette fin. Ce sont des fibres d'acier ou de polymères qui renforcent la structure du ciment, augmentant la résistance du produit dans son ensemble.
Faites attention! À 1 m3 il ne faut pas ajouter plus de 1 kg de fibres à la solution, de sorte que la masse du matériau n’est pas affectée.
Sélection de l'équipement
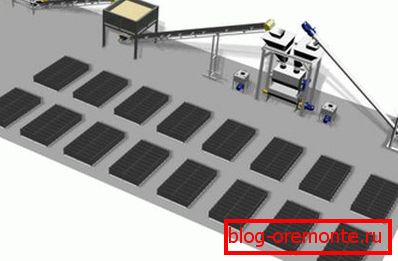
Une installation à l'échelle industrielle pour la production de béton cellulaire est généralement complétée par des installations à cycle complet, dans lesquelles toutes les opérations sont effectuées de manière séquentielle et le mouvement des matières premières est effectué automatiquement. Si nous prévoyons d'organiser la fabrication de façon indépendante, nous pouvons nous en tirer avec un ensemble minimal d'équipements.
Pour faire le travail de leurs propres mains, il faudra:
- Mélangeur - capacité de préparation initiale du mortier à partir de ciment et de sable.
- Pompe de solution.
- Penenerateur - un composant clé de l'ensemble du système, qui injecte de la mousse dans la solution. Généralement, les générateurs de mousse sont fabriqués sur des pompes industrielles du type vortex.
- Compresseur - maintient la pression dans le système. Pour garantir une pression optimale de 8 à 10 bars, vous avez besoin d’un récepteur d’un volume d’au moins 250 litres.
- Réservoir d'eaudans lequel est réalisé le moussage.
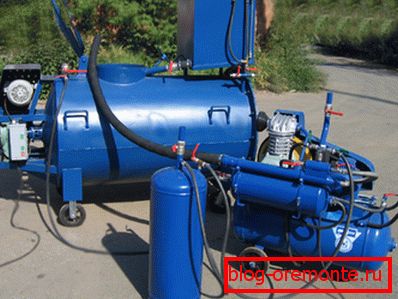
Dans certains cas, il est plus rentable d’acheter une installation intégrée combinant tous ces appareils. Bien entendu, le prix d’une telle unité sera un peu plus élevé, mais son utilisation optimise considérablement le processus de production et réduit les coûts de main-d’œuvre. De bonnes recommandations sont utilisées par les installations domestiques de BAS, Centaurus et leurs analogues avec un coût de 50 à 100 000 roubles.
L’utilisation de tels systèmes permet d’alimenter une solution de béton cellulaire pour la coulée dans le coffrage directement sur l’objet. Si vous envisagez de fabriquer des modules à la pièce, vous aurez également besoin de formes de cassette détachables, ainsi que de plateaux pour le séchage des produits.
Cycle technologique
Préparation de la composition
Donc, l'équipement est prêt, la matière première est achetée - vous pouvez vous mettre au travail.
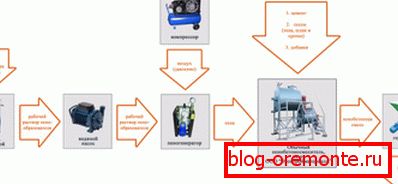
La technologie de fabrication de la mousse permet d’obtenir une solution à haute teneur en air entraîné de différentes manières. Vous pouvez comparer ces méthodes en analysant le tableau ci-dessous:
Technique de production | Caractéristiques du processus |
Mélangeurная | Nous préparons le mortier de ciment et de sable selon la technologie classique, en utilisant un volume d'eau légèrement inférieur au volume nécessaire. Il se forme dans le générateur de mousse par des réactions chimiques une mousse qui est introduite sous pression dans le mélangeur et introduite dans la solution liquide. Le plus souvent, cette technique est mise en œuvre en utilisant des composants moussants de protéines. |
Sec | Le ciment est mélangé avec du sable (cendres, scories broyées) sous forme sèche et passe ainsi dans le mélangeur. La mousse du générateur de mousse, obtenue avec l'addition d'un grand volume d'eau, y est également alimentée. En règle générale, cette technique est mise en œuvre dans la production industrielle, car elle ne porte ses fruits que pour de gros volumes de produits. |
Mélange de pression | La préparation de la solution est effectuée dans une chambre à haute pression. D'abord, il pénètre dans l'eau à partir du générateur de mousse pour le béton mousse, puis les composants secs sont coulés. Après le mélange initial, de l'air est injecté dans la chambre de travail, ce qui contribue à une répartition plus uniforme des pores d'air dans l'épaisseur du matériau. |
Faites attention! Quelle que soit la technologie utilisée, l’instruction recommande d’introduire des additifs modificateurs (modificateurs, durcisseurs, pigments) dans la solution uniquement aux dernières étapes de la réaction.
Obtenir le produit fini

La solution de travail préparée sous pression pénètre dans le manchon de transport.
Et ici nous pouvons agir de deux manières:
- Premièrement, la technologie permet de verser du béton mousse directement dans le coffrage. Dans ce cas, nous posons les composants de manière à ce que le matériau soit suffisant pour remplir le volume requis.
- Deuxièmement, les blocs de construction peuvent être fabriqués à partir de la solution. Ici, le processus sera plus laborieux, nous allons donc le décrire séparément.
La production de modules en béton cellulaire est réalisée comme suit:
- Nous assemblons les moules métalliques en les fixant avec des boulons en acier. L'épaisseur de la paroi du moule doit être suffisante pour empêcher sa déformation sous l'influence de la solution.
- De l'intérieur, nous lubrifions le moule avec de l'huile moteur pour éviter que les blocs finis ne collent au métal et ne se fissurent lors de l'extraction.
- Ensuite, nous effectuons le versement de la solution en répartissant le matériau de manière à éviter la formation de grandes "poches d’air".
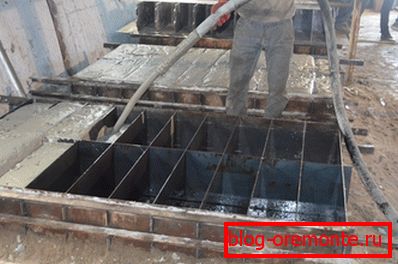
Faites attention! Il est nécessaire de remplir des formulaires à une température ne dépassant pas +15 - 18 0C. Sinon, le jeu de forces ralentira et au moment de l'extraction, les blocs risquent de se défaire.
- Après le versement, effectuez le séchage primaire. À ce stade, le mélange augmente partiellement en raison de la réaction résiduelle et gagne en force.
- Environ deux heures plus tard, nous retirons les blocs du coffrage et les envoyons à la zone de séchage.
- La technologie décrite est typique pour l'utilisation de formes de cassette. Lors de la fabrication d'un bloc de mousse en coulant un monolithe, une grande barre de matériau est découpée dans une scie à ruban avant d'être séchée conformément aux dimensions de conception.
En principe, le séchage peut avoir lieu dans des conditions naturelles. Cependant, il est difficile de contrôler les processus d'hydratation du ciment et le gain de résistance de la solution. C'est pourquoi il est recommandé d'utiliser des chambres de séchage pour la production en série.
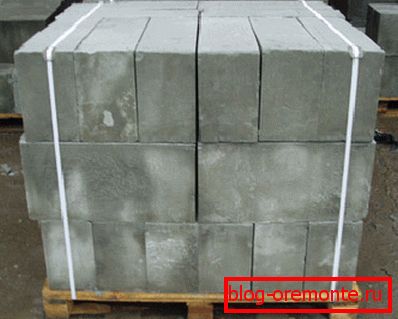
L'unité de séchage est maintenue à une température de 40 à 55 0C. Для полной полимеризации цемента блоки находятся в камере около 6 часов, после чего извлекаются из нее и после суточного «созревания» могут использоваться для строительства и утепления.
Conclusion
L'organisation de la ligne de production pour la production de béton cellulaire n'est possible que sous condition d'une connaissance approfondie du processus technologique. Cependant, les informations présentées dans le texte et dans la vidéo de cet article suffisent amplement pour avoir une idée de la façon dont ce matériel est réalisé. Ainsi, après un peu de pratique et de consultation avec des spécialistes, vous pouvez facilement organiser une telle entreprise et la contrôler avec succès.