Quel est le renforcement du béton utilisé après le coulage
Le béton monolithique, en raison de sa résistance et de sa durabilité élevées, occupe une position de leader parmi tous les matériaux de construction utilisés pour la construction de bâtiments et de structures résidentiels, commerciaux et industriels. Cependant, malgré la grande résistance, la surface du béton monolithique est sujette à la destruction et à l'érosion du fait de l'exposition à divers facteurs externes.
Afin de prévenir les effets nocifs et d’améliorer les performances de ce matériau, le durcisseur liquide pour béton est le plus souvent utilisé. Il est appliqué sur une surface monolithique après durcissement.

Augmenter la résistance de la surface de béton
Afin d'étudier cette question plus en détail, cet article examinera divers types de traitement de surface du béton monolithique, qui visent à augmenter sa résistance et à assurer une protection supplémentaire contre l'influence de facteurs externes.
Nous allons également présenter ici une brève instruction décrivant la technologie d'utilisation de telles substances pendant la construction.
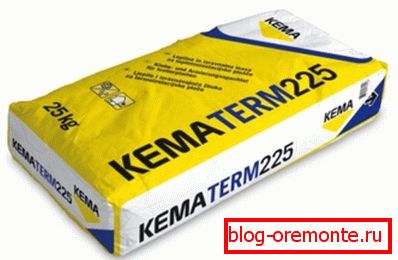
Le but principal des substances durcissantes
Afin de bien comprendre la nécessité et l'opportunité d'utiliser de telles substances, vous devez tout d'abord avoir une idée de la façon dont elles agissent et de leurs fonctions de protection.
Le béton gelé est une structure microporeuse solide constituée de particules d'un liant (ciment) et d'un agrégat de ballast (sable de quartz, pierre concassée, copeaux de granit) liées les unes aux autres. La destruction et l'érosion de la surface du béton sont principalement dues à l'impact abrasif externe, qui conduit à une abrasion progressive et à la formation de poussière.
En outre, lorsque de l'eau et d'autres substances agressives pénètrent dans les pores du matériau, elles cassent sa structure interne, affaiblissent les liaisons du réseau cristallin, ce qui entraîne la formation de fissures et la destruction ultérieure.
Afin de fournir une protection fiable contre de tels phénomènes, les armatures classiques du béton ont généralement les propriétés suivantes:
- Augmente la résistance mécanique de la couche externe de béton grâce au liant, qui pénètre dans l'épaisseur du matériau, maintient ensemble toutes les particules solides, formant une surface monolithique uniforme.
- Procure une imperméabilisation supplémentaire de la couche externe, empêchant ainsi la pénétration d'eau et de substances agressives dans l'épaisseur du matériau.
- Augmente la résistance à l'usure et la résistance à l'abrasion du matériau et empêche également la formation de poussière et de fissures sur sa surface pendant le fonctionnement
- Après le séchage est une bonne base pour appliquer des peintures spéciales et d’autres matériaux de finition.
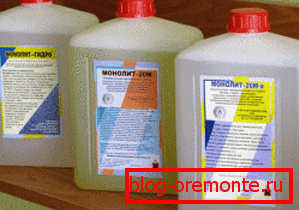
Astuce! De nombreux constructeurs connaissent bien le phénomène de fissuration de la surface d'une chape en béton lors de la solidification. L'utilisation de durcisseurs chimiques immédiatement après la prise de la solution réduit considérablement le risque de telles fissures.
Variétés de durcisseurs de béton
Actuellement, il existe un grand nombre de types différents de substances durcissantes, chacune ayant ses avantages et ses inconvénients et pouvant être utilisée dans certaines conditions.
- Une armature sèche pour un sol en béton est un mélange de ciment de haute qualité (ciment Portland de haute qualité), de granulats minéraux ayant une résistance élevée à l'abrasion (copeaux de granit ou de corindon) et d'additifs chimiques tensioactifs qui améliorent l'adhésion de la composition de travail à la solution de béton. La principale qualité distinctive des mélanges secs est son prix relativement bas, comparé à d'autres types de durcisseurs.
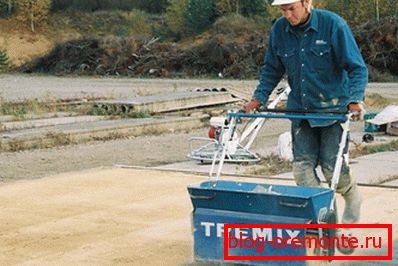
- En règle générale, l’imprégnation par durcissement chimique est une solution aqueuse de certains sels et oxydes qui dispersent dans l’eau les liaisons cristallines du ciment avec des particules de granulats de ballast (sable, gravier, pierre concassée) et réduisent l’absorption d’humidité après la solidification de la solution.
- Compositions à deux composants à base de résines époxy, pénétrant dans la solution congelée, les particules solides sont liées les unes aux autres au cours du processus de polymérisation, ce qui leur permet de former une surface monolithique imperméable.
- Les compositions pénétrantes à base de résines de polyuréthanne agissent de la même manière que les résines époxy, mais après polymérisation, elles résistent à des contraintes de compression plus faibles.
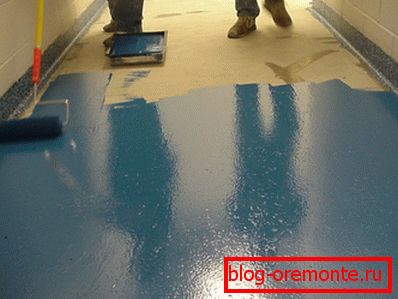
Astuce! Pour assurer la réaction normale du béton avec tout type de durcisseur, la température de la surface monolithique ne doit pas être inférieure à + 10 ° C, tandis que la température critique minimale pour l'utilisation de telles compositions est de + 5 ° C.
Méthode d'utilisation
La technologie d'utilisation de différents types de compositions présente une différence significative entre les arcs les uns des autres et est généralement réalisée à différentes étapes de la solidification d'une surface monolithique.
- Les mélanges durcissant à sec doivent être appliqués sur un mortier de béton fraîchement coulé, immédiatement après sa mise en place, sans craindre de perturber l'intégrité de sa surface. La composition doit être répartie sur toute la surface en une couche uniforme dont l’épaisseur est indiquée dans le mode d’emploi. Ensuite, utilisez un outil de scellement manuel ou électrique.
- Un durcisseur chimique liquide pour le sol en béton est appliqué après la prise partielle du mortier. En règle générale, cela se produit 3 à 7 heures après le coulage du monolithe. Pour l'application, vous pouvez utiliser un pistolet pneumatique, ainsi qu'un rouleau de peinture ou un pinceau large avec un long manche.
- Les compositions pénétrantes à base d'époxy ou de polyuréthane ne peuvent être utilisées qu'après solidification complète et séchage de la surface monolithique. Lors de la préparation d'une composition époxy avec vos propres mains, vous devez respecter scrupuleusement les proportions du durcisseur et de la base, indiquées dans le mode d'emploi.

Astuce! En règle générale, la viabilité des compositions à base de résines époxydes est limitée dans le temps; elles doivent donc être préparées par petites portions, en quantité pouvant être consommée dans les 20 à 30 minutes de travail.
Conclusion
Après avoir lu cet article, il apparaît clairement qu’il existe un grand nombre de composés chimiques et minéraux variés avec lesquels vous pouvez indépendamment augmenter la résistance et la durabilité des surfaces de béton monolithique.
Pour plus d'informations sur ce problème, vous pouvez regarder la vidéo dans cet article ou lire des documents similaires sur notre site Web.